Different Types of Stern Tube Seals
Arguably one of the most critical shipboard systems is the seal which keeps sea water out, and allows the propulsion shaft to continue spinning, the Stern Tube Seal. Without it, as soon as the ship was launched, water would travel up the stern tube or through the transom directly into the ship and it would sink.
It would be easy enough to seal up the stern tube itself, except for the enormous rotating shaft that has to pass through it to allow the ships propulsion system to move the vessel through the water. The seals have to be rugged, long lasting, and hold up to a myriad of varying circumstances and conditions.
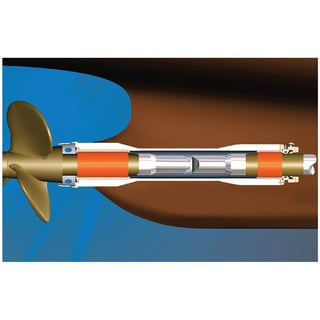
There are a few types of major stern tube seals on the market today all with one job, to keep the ship moving through the water, and the water out of the ship. These include;
- labyrinth Seals
- Mechanical Face Seals
- Packing Type
Common Stern Tube Seal Types
Labyrinth Seals
The general working principle of Labyrinth seals is to create a series of barriers that gradually reduce pressure such that the final seal is not subject to a large volume of sealing media at these higher pressures. The purposeful long and winding path that the sealing liquid must follow can then be sealed watertight by conventional means such as an O-ring or lip seal.
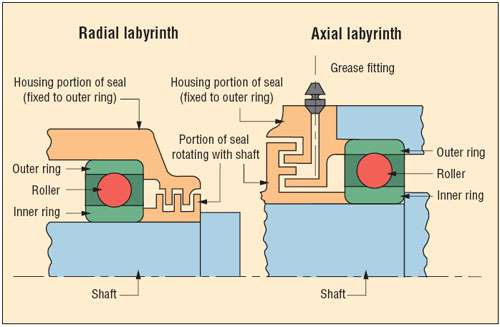
While an effective means of sealing, this method has inherent issues with longevity as the final seals are commonly elastomer based and in contact with rotating equipment at all times thus subject to friction wear. Elastomers have a limit in terms of surface speed capabilities, which diminishes over time. Incredibly tight tolerances are also required as the passages begin to narrow, driving manufacturing cost and creating installation and premature failure challenges.
Mechanical Face Seals
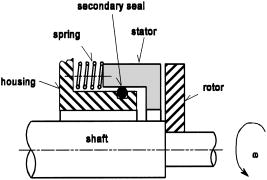
The common issues with the above labyrinth seals of failure due to friction has been solved by the mechanical face seal…sort of. In order to handle the frictional loading, mechanical face seals get around the heat caused by frictional loading by using the sealing media for a cooling and friction reducing effect. Using a phenomenon known as hydrodynamic lift, spinning faces allow a small, sometimes microscopic layer of sealing fluid to ride between the faces thus reducing, or in some cases, nearly eliminating friction. Where friction is reduced, heat is reduced, and where heat is reduced, so is wear. This means that mechanical face seals are designed to run for long periods of time at high speeds. Sounds like a slam dunk, right?
Wrong. Not every two materials are compatible with one another when talking about counter rotating faces. To this same point, various speeds of rotating equipment create different hydrodynamic lift profiles which all must be accounted for to ensure that the seal continues to keep sealing fluid out, and that friction and heat do not cause damage. To understand friction loads and ideal operating parameters we must consult Stribek curves. A basic example of a Stribek curve is shown below.
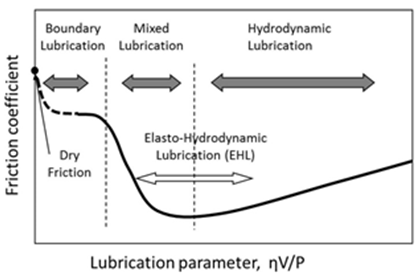
Stribek Curves help determine the areas of the lowest friction and help engineers choose face materials and design seal cross sections. The lowest friction areas lie in the Elasto-Hydrodynamic region and is the ideal criteria for a long last, high performance mechanical face seal. To understand more about Stribek Curves, and the study of friction and wear, also known as Tribology, we conducted several tests with the assistance of LSU Professor Dr. Michael Khonsari where a number of materials were subjected to varying fluid media and pressures to better understand the friction and wear relationship that a pair of materials exhibits.
Similar to labyrinth seals, mechanical face seals require additional support materials such as flushing water, oil and grease to keep them running. Many systems use an oil lubrication bath to keep faces cool, however these oil filled seals are known to fail and are a leading cause of pollution of today’s oceans. This challenge has been overcome by developing water cooled mechanical face seals using proprietary ultra-low friction face sealing materials that do not require the use of any oil and is 100% environmentally friendly. The materials chosen are also much more robust than some of the common ceramic based materials which are prone to breakage and cracking in harsh usage conditions.
Packing Type
Perhaps the oldest and most utilized system of sealing of rotating equipment is through the use of packing. Materials such as fibrous rope, oakum, carbon and graphite based materials have been used for as long as there have been rotating shafts driving ships through the world’s oceans. There have been great advances in the materials created for use in packing applications, however these systems limit operation speed profiles, require increased maintenance and must be checked and re-packed at frequent intervals. While generally easy to perform these tasks, over the life of a ship material and labor costs to do so can dramatically increase operating costs and downtime.
This method can also cause damage to the shafting itself as it is always in contact with rotating equipment and can begin to breakdown the materials and cause galling and pitting as sealing media beings to corrode the rotating shaft. In these cases, more packing will not necessarily slow or stop increasing leaks, and shafting must be replaced. The cross section below shows the arrangement that Duramax Marine (www.duramaxmarine) uses in their packing style shaft sealing system.
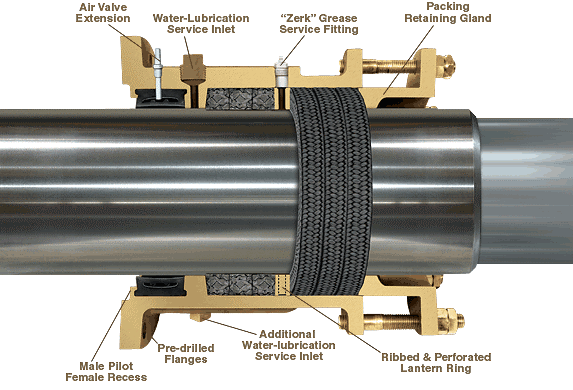
The principles of packing are generally straight forward. A packing material is stuffed in a cavity around the rotating equipment and placed under axial compression to create a friction seal between the housing body and the rotating equipment. Eventually over time the material will breakdown and wear away. This is most noticeable as drips or increased seal leakage become present, at which time the old packing is removed and new packing is inserted. Repeat regularly for 30 to 40 years, and you have yourself a packing type seal.
How to Choose
With all of the options available on the market today, which is the right one for you, your vessel or your customer? A number of parameters come into play such as shaft size, operating RPM, relative shaft motion, draft pressure. A mechanical face seal may seem like the robust design, but if you only have a small 2-3" diameter shaft that sees only a few hundred hours of operation a year and you can get away with a more affordable option like a Duramax Packing type seal, that may be a better route. Or you may have a system with incredibly high shaft speeds, and allows some amount of leak with regularly scheduled maintenance and you can get away by using a labyrinth seal.
At the end of the day, the application will dictate the most suitable option. Feel free to contact me with any questions.